Сварочные соединения являются неотъемлемой частью большинства конструкций в машиностроении, строительстве, судостроении и других отраслях. От их качества напрямую зависит безопасность и долговечность объектов. Однако, несмотря на высокую квалификацию специалистов и использование современных технологий сварки, дефекты в соединениях могут возникать на разных этапах производства, эксплуатации и в условиях внешних воздействий. Поэтому важной задачей является своевременное выявление таких дефектов, не нарушая целостности самих конструкций. Для этой цели используются методы неразрушающего контроля сварных соединений.
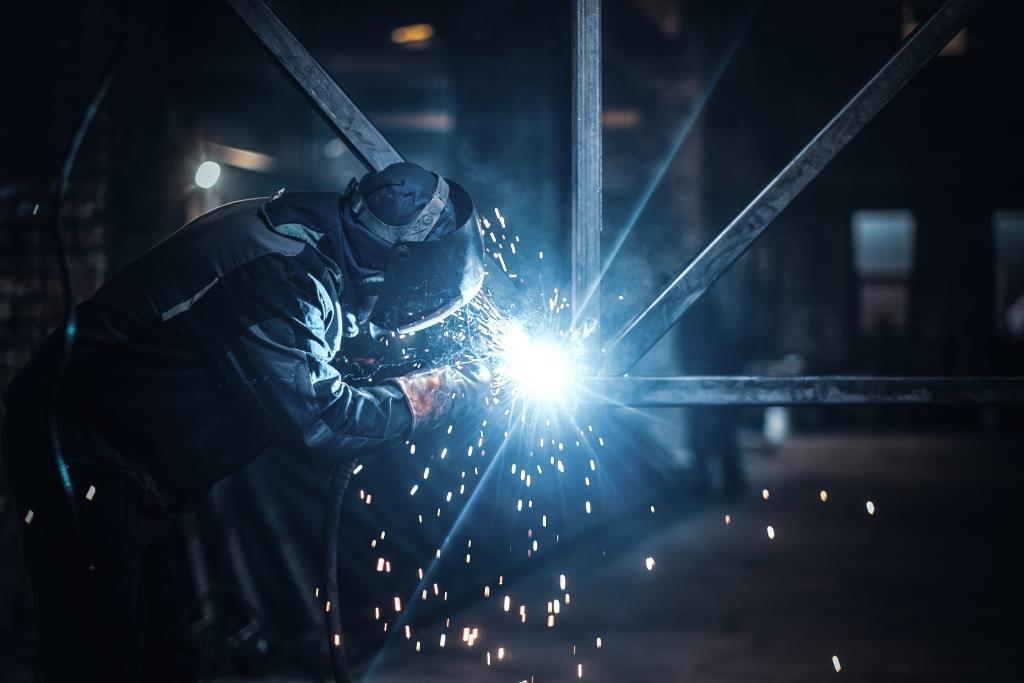
Методы неразрушающего контроля (НК) позволяют проводить тщательную проверку сварных швов и других критичных элементов конструкции без их повреждения. Это обеспечивает не только высокую безопасность эксплуатации объектов, но и сокращение затрат на демонтаж или восстановление конструкций. В статье рассматриваются основные методы НК, их особенности и области применения, а также значимость этих методов для обеспечения надежности и долговечности сварных соединений.
Современные методы неразрушающего контроля сварных соединений
Методы неразрушающего контроля сварных соединений применяются в различных ситуациях, когда требуется оценить качество сварных швов и убедиться в их безопасности и надежности. Они используются как сразу после завершения сварочных работ, для проверки соответствия качества соединений установленным требованиям, так и в процессе эксплуатации объектов, для оценки их технического состояния и продления срока службы. Важно, что неразрушающий контроль также проводится в рамках технического диагностирования, экспертиз промышленной безопасности и других мероприятий, направленных на профилактику аварий и обеспечение безопасности.
Выбор конкретных методов неразрушающего контроля сварных соединений для определенного объекта определяется техническим руководителем организации, проводящей контроль, с учетом действующих Федеральных Норм и Правил, в частности, Федеральных Норм и Правил № 535. Эти документы регулируют требования к проведению контроля в различных отраслях и обеспечивают стандартизацию процедур.
Выбор конкретных методов неразрушающего контроля сварных соединений для определенного объекта определяется техническим руководителем организации, проводящей контроль, с учетом действующих Федеральных Норм и Правил, в частности, Федеральных Норм и Правил № 535. Эти документы регулируют требования к проведению контроля в различных отраслях и обеспечивают стандартизацию процедур.
Нормативные документы, регулирующие проведение неразрушающего контроля сварных соединений
Проведение неразрушающего контроля (НК) сварных соединений строго регламентируется рядом нормативных документов, таких как ГОСТы, НТД (нормативно-технические документы) и РД (руководящие документы). Эти стандарты подробно описывают классификацию видов и методов НК сварных соединений, а также порядок их применения. В документах указываются условия и область применения различных методов контроля, требования к контрольно-измерительной аппаратуре, средства контроля и стандартные образцы, а также правила подготовки и проведения контроля, оформление его результатов и другие важные аспекты.
Основной принцип всех методов неразрушающего контроля сварных соединений
Главной целью всех методов НК сварных соединений является проверка соответствия параметров объекта установленным техническим требованиям, которые прописаны в НТД и РД. В процессе контроля выявляются дефекты сварных швов, которые могли возникнуть на разных этапах: в ходе производства, при монтаже оборудования или в процессе эксплуатации. Результаты НК помогают определить техническое состояние объекта и позволяют принять решения о его дальнейшей эксплуатации.
Важно, что неразрушающий контроль выполняется на месте нахождения объекта, не нарушая его эксплуатационной пригодности. Таким образом, целостность конструкции сохраняется, и объект продолжает оставаться готовым к использованию.
Типы дефектов сварных соединений
Сварные соединения могут содержать различные дефекты, такие как:
В зависимости от поставленных задач для каждого случая выбираются соответствующие методы НК сварных соединений. Часто для более точной и надежной оценки качества сварных швов применяются комбинированные методы, сочетающие различные виды контроля. Это позволяет снизить вероятность ошибки и повысить точность диагностики, а также дает более полное представление о состоянии объекта. Комбинированное использование различных методов НК делает процесс контроля более эффективным и результативным.
Проведение неразрушающего контроля (НК) сварных соединений строго регламентируется рядом нормативных документов, таких как ГОСТы, НТД (нормативно-технические документы) и РД (руководящие документы). Эти стандарты подробно описывают классификацию видов и методов НК сварных соединений, а также порядок их применения. В документах указываются условия и область применения различных методов контроля, требования к контрольно-измерительной аппаратуре, средства контроля и стандартные образцы, а также правила подготовки и проведения контроля, оформление его результатов и другие важные аспекты.
- ГОСТ 17635-2018, регулирующий проведение неразрушающего контроля сварных соединений.
Основной принцип всех методов неразрушающего контроля сварных соединений
Главной целью всех методов НК сварных соединений является проверка соответствия параметров объекта установленным техническим требованиям, которые прописаны в НТД и РД. В процессе контроля выявляются дефекты сварных швов, которые могли возникнуть на разных этапах: в ходе производства, при монтаже оборудования или в процессе эксплуатации. Результаты НК помогают определить техническое состояние объекта и позволяют принять решения о его дальнейшей эксплуатации.
Важно, что неразрушающий контроль выполняется на месте нахождения объекта, не нарушая его эксплуатационной пригодности. Таким образом, целостность конструкции сохраняется, и объект продолжает оставаться готовым к использованию.
Типы дефектов сварных соединений
Сварные соединения могут содержать различные дефекты, такие как:
- Дефекты формы шва — отклонения от правильной геометрии сварного соединения.
- Наружные и внутренние дефекты — трещины, поры, включения, недостаточная или избыточная сварка, которые могут быть видимыми на поверхности или скрытыми внутри шва.
В зависимости от поставленных задач для каждого случая выбираются соответствующие методы НК сварных соединений. Часто для более точной и надежной оценки качества сварных швов применяются комбинированные методы, сочетающие различные виды контроля. Это позволяет снизить вероятность ошибки и повысить точность диагностики, а также дает более полное представление о состоянии объекта. Комбинированное использование различных методов НК делает процесс контроля более эффективным и результативным.
Визуально-измерительный контроль (ВИК)
Визуально-измерительный контроль (ВИК) является основным и первичным методом неразрушающего контроля. Он включает в себя простой внешний осмотр сварных соединений с использованием базовых измерительных инструментов, таких как рулетка, штангенциркуль и шаблоны. Это метод с минимальными затратами, который позволяет оперативно выявить наружные дефекты сварных швов. Среди них могут быть:
Кроме того, к этому методу можно отнести и визуально-оптический контроль, который осуществляется с использованием увеличительных стекол или микроскопов. Этот подход позволяет детально исследовать сварные швы и обнаружить даже самые мелкие поверхностные дефекты, которые могут быть не видны невооруженным глазом.
- наличие шлака или загрязнений;
- брызги металла;
- ржавчина и другие загрязненные участки;
- сквозные прожоги или трещины;
- подрезы и дефекты геометрии шва;
- остатки флюса и другие внешние повреждения.
Кроме того, к этому методу можно отнести и визуально-оптический контроль, который осуществляется с использованием увеличительных стекол или микроскопов. Этот подход позволяет детально исследовать сварные швы и обнаружить даже самые мелкие поверхностные дефекты, которые могут быть не видны невооруженным глазом.
Ультразвуковая диагностика или дефектоскопия (УЗД)
Ультразвуковая диагностика, также известная как ультразвуковой контроль (УЗК), представляет собой набор эхо-акустических методов неразрушающего контроля сварных соединений, применяемых для материалов с различной плотностью. Этот метод использует ультразвуковые волны, которые проходят через сварной шов и отражаются от различных дефектов, таких как трещины, поры, пустоты и другие неоднородности. Для проведения ультразвуковой дефектоскопии применяются специальные приборы — ультразвуковой преобразователь и дефектоскоп, которые анализируют отраженные сигналы и определяют местоположение и размер дефектов.
Ультразвуковая дефектоскопия обладает рядом преимуществ, среди которых — высокая точность и способность обнаруживать дефекты на глубине, а также её безопасность по сравнению с рентгеновским контролем. В отличие от рентгеновских методов, ультразвуковая диагностика не использует ионизирующее излучение, что делает её более безопасной для персонала и окружающей среды. Благодаря этим особенностям УЗД стало одним из самых популярных и эффективных методов неразрушающего контроля сварных соединений.
Ультразвуковая дефектоскопия обладает рядом преимуществ, среди которых — высокая точность и способность обнаруживать дефекты на глубине, а также её безопасность по сравнению с рентгеновским контролем. В отличие от рентгеновских методов, ультразвуковая диагностика не использует ионизирующее излучение, что делает её более безопасной для персонала и окружающей среды. Благодаря этим особенностям УЗД стало одним из самых популярных и эффективных методов неразрушающего контроля сварных соединений.
Магнитопорошковый контроль (магнитный) (МПД)
Магнитопорошковый контроль (МПД) является одним из эффективных методов неразрушающего контроля, который используется для обнаружения поверхностных и подповерхностных дефектов сварных соединений, таких как трещины, непровары, шлаковые и флюсовые включения, окисные включения, подрезы и другие повреждения.
Принцип действия:
Метод основан на использовании магнитных полей для выявления дефектов в материалах, обладающих магнитными свойствами. При намагничивании объекта, на его поверхности создаются неоднородные магнитные поля, которые в районе дефектов (например, трещин или пор) усиливаются. Это приводит к образованию индикаторных рисунков — скоплений магнитных частиц, которые визуально или с помощью оптических приборов могут быть зафиксированы. Форма этих скоплений точно соответствует контурам обнаруженных дефектов.
Методика контроля:
Особенности метода:
Магнитопорошковый контроль применяется только для объектов с магнитными свойствами. Однако, он также может быть использован для проверки изделий с немагнитным покрытием (например, краска, лак, хром, медь, кадмий, цинк и другие покрытия), при толщине покрытия не более 40-50 мкм. В этом случае, дефекты могут быть обнаружены без значительного снижения эффективности метода.
МПД представляет собой оперативный и эффективный способ контроля, который проводится непосредственно на месте нахождения объекта и не нарушает его эксплуатационных характеристик. Метод является неразрушающим и позволяет быстро получить результаты.
Ограничения метода:
Магнитопорошковый контроль относится к индикаторным (неизмерительным) методам, что означает, что он не предоставляет информации о точных размерах дефектов, таких как их длина, глубина или ширина. Для получения более детализированных данных о характеристиках дефектов, комбинируются МПД и визуально-измерительный контроль (ВИК), что позволяет значительно повысить точность оценки состояния сварных соединений.
Принцип действия:
Метод основан на использовании магнитных полей для выявления дефектов в материалах, обладающих магнитными свойствами. При намагничивании объекта, на его поверхности создаются неоднородные магнитные поля, которые в районе дефектов (например, трещин или пор) усиливаются. Это приводит к образованию индикаторных рисунков — скоплений магнитных частиц, которые визуально или с помощью оптических приборов могут быть зафиксированы. Форма этих скоплений точно соответствует контурам обнаруженных дефектов.
Методика контроля:
- Подготовка поверхности — перед началом контроля поверхность изделия очищается от загрязнений, окалины, масла и других посторонних веществ.
- Намагничивание изделия — сварное соединение или объект подвергается намагничиванию с использованием постоянных или переменных магнитных полей.
- Нанесение магнитного порошка — на поверхность объекта наносится магнитный порошок или суспензия.
- Осмотр поверхности — с помощью визуального осмотра или оптических приборов оценивается состояние поверхности, фиксируются индикаторные рисунки.
- Оценка индикаторных рисунков — результаты осмотра анализируются, и на основе их формы и протяженности делаются выводы о наличии и характере дефектов.
- Расшифровка результатов — интерпретация полученных данных и определение наличия дефектов на основании индикаторных рисунков.
Особенности метода:
Магнитопорошковый контроль применяется только для объектов с магнитными свойствами. Однако, он также может быть использован для проверки изделий с немагнитным покрытием (например, краска, лак, хром, медь, кадмий, цинк и другие покрытия), при толщине покрытия не более 40-50 мкм. В этом случае, дефекты могут быть обнаружены без значительного снижения эффективности метода.
МПД представляет собой оперативный и эффективный способ контроля, который проводится непосредственно на месте нахождения объекта и не нарушает его эксплуатационных характеристик. Метод является неразрушающим и позволяет быстро получить результаты.
Ограничения метода:
Магнитопорошковый контроль относится к индикаторным (неизмерительным) методам, что означает, что он не предоставляет информации о точных размерах дефектов, таких как их длина, глубина или ширина. Для получения более детализированных данных о характеристиках дефектов, комбинируются МПД и визуально-измерительный контроль (ВИК), что позволяет значительно повысить точность оценки состояния сварных соединений.
Капиллярный метод контроля сварных соединений
Капиллярный метод контроля представляет собой эффективный способ обнаружения невидимых наружных и внутренних дефектов сварных соединений. Основной принцип этого метода заключается в использовании жидкостей с высокой вязкостью (индикаторов), которые способны проникать в самые мелкие трещины и поры в сварных швах, благодаря капиллярному эффекту.
Процесс контроля включает нанесение на поверхность сварного соединения специального реагента, называемого проявителем. Этот реагент вступает в контакт с индикатором, заполнившим дефекты, и изменяет свой цвет в местах их обнаружения, что позволяет визуально выделить проблемные участки.
Капиллярный метод является недорогим и простым в применении, однако его основное ограничение заключается в том, что он не подходит для выявления скрытых внутренних дефектов, так как работает только с поверхностными нарушениями. Тем не менее, данный метод широко используется для обнаружения мелких поверхностных дефектов, таких как трещины, поры, подрезы или другие дефекты, которые могут возникать на внешней поверхности сварного шва.
Процесс контроля включает нанесение на поверхность сварного соединения специального реагента, называемого проявителем. Этот реагент вступает в контакт с индикатором, заполнившим дефекты, и изменяет свой цвет в местах их обнаружения, что позволяет визуально выделить проблемные участки.
Капиллярный метод является недорогим и простым в применении, однако его основное ограничение заключается в том, что он не подходит для выявления скрытых внутренних дефектов, так как работает только с поверхностными нарушениями. Тем не менее, данный метод широко используется для обнаружения мелких поверхностных дефектов, таких как трещины, поры, подрезы или другие дефекты, которые могут возникать на внешней поверхности сварного шва.
Радиографический контроль сварных швов (РК)
Радиографический контроль сварных швов, также известный как просвечивание рентгеновскими лучами, представляет собой один из самых точных и эффективных методов неразрушающего контроля. Этот метод позволяет детально изучить внутреннюю структуру сварного шва и выявить скрытые дефекты, такие как полости, непровары, инклюзии или другие дефекты, которые невозможно обнаружить с помощью визуального контроля или других методов.
Принцип радиографического контроля заключается в использовании рентгеновских или гамма-лучей для просвечивания сварных соединений. Радиационное излучение проникает через металл и, в зависимости от плотности и структуры материала, часть излучения поглощается или проходит через объект. Образующееся изображение, которое фиксируется на фотопленке или цифровом детекторе, позволяет выявить дефекты, скрытые внутри сварного шва.
Радиографический контроль применяется в тех случаях, когда требуется высокая точность и надежность, и когда даже малый процент брака может привести к серьезным последствиям. Этот метод широко используется в аэрокосмической, судостроительной, нефтегазовой и других отраслях, где качество сварных соединений критически важно.
Однако одним из основных недостатков радиографического контроля является необходимость соблюдения строгих мер безопасности, поскольку метод включает использование радиационного излучения. Это требует дополнительных затрат времени и ресурсов на организацию безопасных условий работы, а также на обучение и сертификацию персонала, работающего с радиографическим оборудованием.
Принцип радиографического контроля заключается в использовании рентгеновских или гамма-лучей для просвечивания сварных соединений. Радиационное излучение проникает через металл и, в зависимости от плотности и структуры материала, часть излучения поглощается или проходит через объект. Образующееся изображение, которое фиксируется на фотопленке или цифровом детекторе, позволяет выявить дефекты, скрытые внутри сварного шва.
Радиографический контроль применяется в тех случаях, когда требуется высокая точность и надежность, и когда даже малый процент брака может привести к серьезным последствиям. Этот метод широко используется в аэрокосмической, судостроительной, нефтегазовой и других отраслях, где качество сварных соединений критически важно.
Однако одним из основных недостатков радиографического контроля является необходимость соблюдения строгих мер безопасности, поскольку метод включает использование радиационного излучения. Это требует дополнительных затрат времени и ресурсов на организацию безопасных условий работы, а также на обучение и сертификацию персонала, работающего с радиографическим оборудованием.
Другие способы неразрушающего контроля
Методы неразрушающего контроля (НК) сварных соединений не ограничиваются только теми, которые были рассмотрены ранее. В зависимости от специфики производства и сложности объектов, промышленные предприятия могут применять более высокотехнологичные и специализированные методики. Для этого часто создаются отдельные лаборатории, оснащенные диагностическим оборудованием, что особенно характерно для крупных промышленных предприятий с автономными участками эксплуатации. В соответствии с ГОСТами, наряду с основными методами, широко применяются и другие, более сложные способы НК:
Каждый из этих методов имеет свои особенности и применяется в зависимости от конкретных требований, таких как тип материала, размер объекта и степень критичности дефектов. В сочетании с основными методами, эти дополнительные подходы обеспечивают более глубокое и детальное исследование качества сварных соединений, что особенно важно для объектов, работающих в экстремальных условиях или требующих высокой надежности.
- Вихретоковый контроль — этот метод основан на анализе взаимодействия электромагнитных полей с материалом, которое происходит при прохождении электрического тока через сварные соединения. Вихревые токи, возникающие в проводящих материалах, помогают выявить поверхностные и подповерхностные дефекты, такие как трещины, коррозию или износ. Этот метод особенно эффективен для проверки деталей из проводящих материалов, таких как металлы.
- Тепловой контроль — метод основан на принципе преобразования инфракрасного излучения в видимый спектр. Тепловой контроль позволяет обнаружить аномалии в температурном поле сварного соединения, которые могут быть связаны с дефектами, такими как непровары, трещины или изменения в структуре материала. Этот метод широко используется для контроля качества сварных швов на горячих и холодных участках.
- Использование микротвердометров — этот метод применяется для измерения твердости материала сварных соединений на микроскопическом уровне. Микротвердометры позволяют провести локальное измерение твердости сварного шва и определить его структурные изменения, которые могут свидетельствовать о наличии дефектов, таких как хрупкость или изменения в химическом составе шва.
- Методы экспресс-контроля, такие как TOFD (дифракционно-временной метод) — это высокоэффективный метод, используемый для обнаружения подповерхностных дефектов в сварных швах. Метод TOFD основан на принципе дифракции ультразвуковых волн, что позволяет точно определять расположение и размер дефектов в реальном времени, с минимальными временными затратами на проведение контроля.
Каждый из этих методов имеет свои особенности и применяется в зависимости от конкретных требований, таких как тип материала, размер объекта и степень критичности дефектов. В сочетании с основными методами, эти дополнительные подходы обеспечивают более глубокое и детальное исследование качества сварных соединений, что особенно важно для объектов, работающих в экстремальных условиях или требующих высокой надежности.